Intelligent Transparency, Support and Analysis
Exact process documentation with QUAT²RO® Monitoring
QUAT2RO® Monitoring as a tool for process monitoring is a central component of the QUAT²RO® System Intelligence in addition to Remote Service and supplementary analysis options. Thanks to its fully automatic, continuous recording and documentation of the entire packing processes, QUAT²RO® Monitoring supports the user effectively and proactively and so allows comprehensive process optimization. All relevant data are recorded in real time and packaged in clear, individually configurable progress reports. Visualized production information and maintenance notes can be called up at any time and from anywhere in the world via a computer, tablet or smartphone – thus allowing the greatest possible transparency for a secure process.
Preventive maintenance for optimum planning
In addition to data on the plant efficiency and utilization, the digital service product from HAVER & BOECKER also contributes to continuous process optimization by providing detailed maintenance information. Predefined threshold values for recommended maintenance intervals, depending on the number of units or operating hours, can be quickly and easily adjusted by the user to suit individual requirements and experience. For plant manager Detlef Ströse, this is an important argument for using QUAT²RO® Monitoring.
More efficiency, lower costs
Thanks to QUAT²RO® Monitoring, not only exact total production figures are now available, but so are the specific performance and weight data of each individual filling spout and any possible causes of faults: "Deviations such as the reduced output of a particular spout can hardly be detected without the program, but they cost money! With QUAT²RO® Monitoring, such irregularities can now be detected at a glance and removed in a targeted manner." Fewer rejects, more productivity and saving valuable troubleshooting time are the results. The customized maintenance information also guarantees further optimization potential.
QUAT²RO® Remote Service: The direct line to a service technician
With Remote Service, which is also included in QUAT²RO® System Intelligence, users also create the basis for fast, direct and uncomplicated support from HAVER & BOECKER service technicians. This is how faults or inefficient processes in packing lines can be remedied in up to 90 percent of the cases without any cost-intensive on-site operations or long downtimes. "The service technicians can usually quickly locate the causes of faults with remote maintenance and remove them directly," says Detlef Ströse. "This not only reduces downtimes, but also gives me and the entire team the security of knowing that support is always available should worse come to the worst."
Quick and easy to access QUAT²RO® System Intelligence
The path to more transparency, efficiency and reliability through the QUAT²RO® System Intelligence digital service portfolio worked smoothly for the Baumit plant in Oer-Erkenschwick: "Once our IT had created the necessary technical requirements within our system, the installation of the pre-installed QUAT²RO® kit by HAVER & BOECKER service technician Andreas Hansow was completed within a few hours. "For us, the QUAT²RO® System Intelligence has really paid off. We are seeing clear added value without any effort on our part as users," Detlef Ströse emphasizes. "I can and will definitely recommend this to my colleagues!"
How do I get my QUAT²RO® System Intelligence?
Step 1: Contact us and together we will analyze the requirements of your existing system.
Step 2: Our experts configure a customized solution for your system and send you a quote.
Step 3: Together we plan the installation, the commissioning of the system, the training of your employees and the final acceptance.
This could also interest you:
Klaus Siewecke
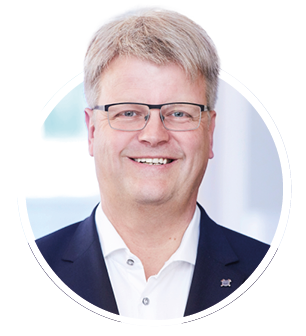
Klaus Siewecke
Manager Customer Support
Andreas Hansow
![[Translate to English:]](/fileadmin/HaverBoecker/DieMaschinenfabrik/01_graphic/Neue_Profilbilder/andreas-hansow.png)
Andreas Hansow
Service
Dennis Friemel
![[Translate to English:]](/fileadmin/HaverBoecker/DieMaschinenfabrik/01_graphic/Neue_Profilbilder/dennis-friemel.png)
Dennis Friemel
Product Manager Electrical Engineering