Intelligent bagging with HAVER & BOECKER
Customer proximity, foresight and solid industrial expertise: HAVER & BOECKER OHG, headquartered in Oelde, Germany has always demonstrated innovative strength in the innovation and further development of trend-setting process solutions. The company's own HAVER & BOECKER Institute and HAVER Innovation Management are dedicated to the constant need for optimization from demanding customers from all over the world. Using decades of experience in close coordination with its customers, the real fulfillers of wishes are created and become the innovations of tomorrow. With the development of a highly efficient bag scanner, the packing specialists are now creating the best conditions for the "intelligent bag" and more efficient results for filling loose, bulk goods.
Together for progress
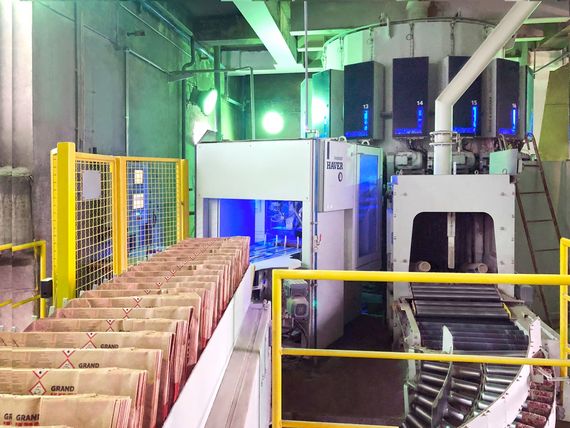
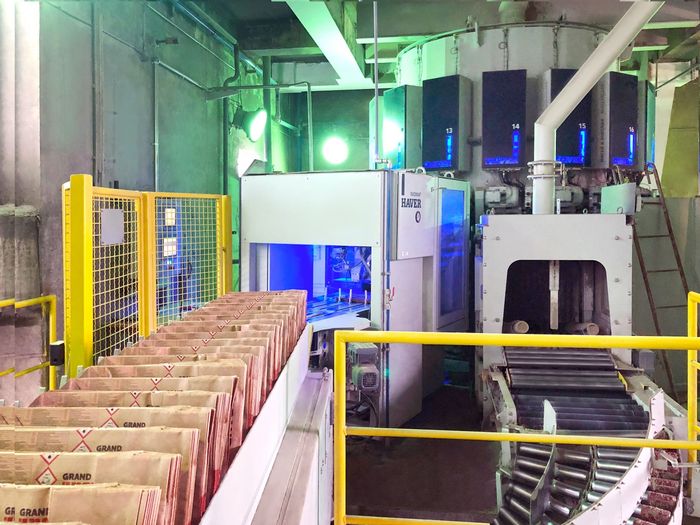
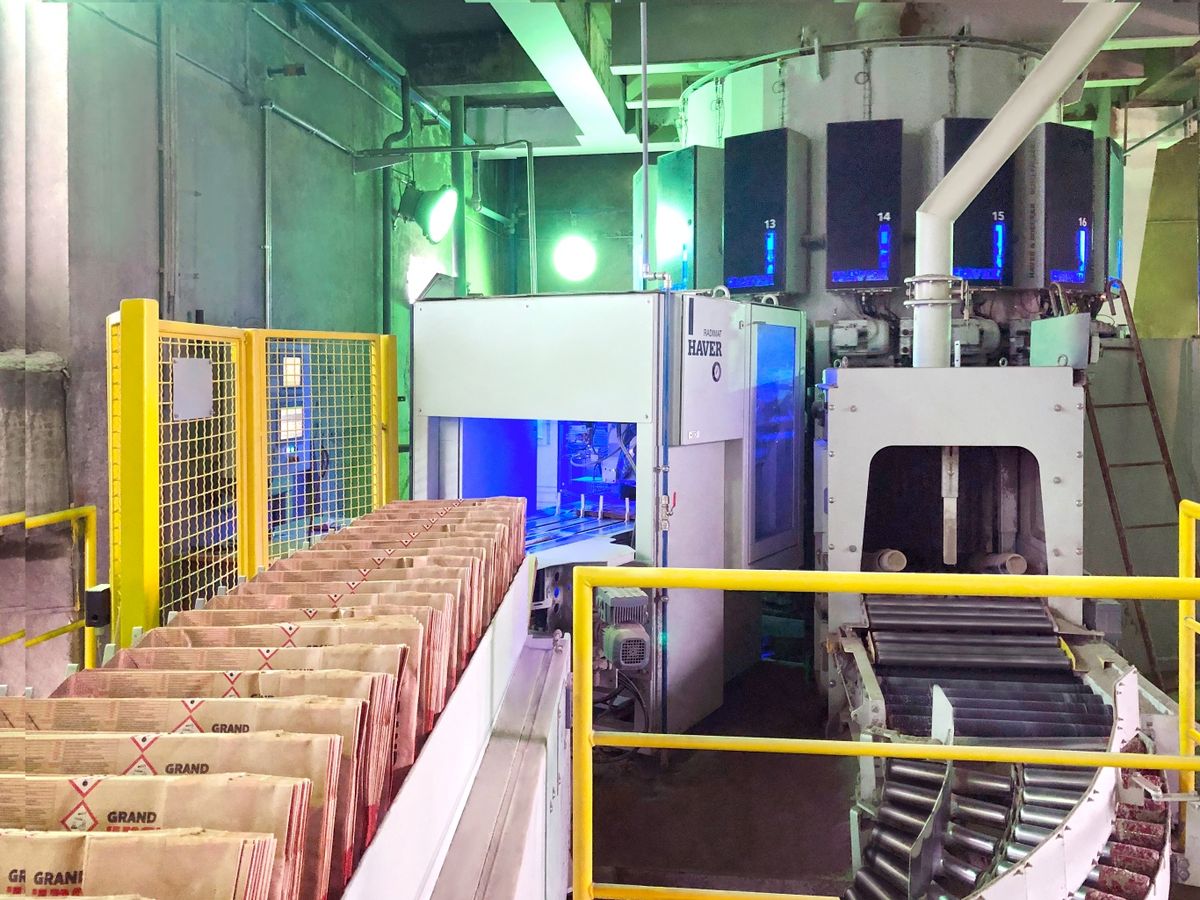
In Našice, Croatia, the HAVER & BOECKER team found the right partner for the implementation and maturation of the first bag scanner. "At NEXE d.d., Croatia's second largest cement producer and the leading member of the internationally successful NEXE Group, everything really fits well,” report Mirko Hoffmann, Sales Head Cement, and Alexander Hering as the responsible sales representative. "NEXE d.d. is the only cement producer in Croatia that is privately owned and has flexible, well-functioning and reliable structures." These advantages are reinforced by the special innovative spirit of its long-time CEO, Ivan Ergović. "In our previous cooperation, we had already come to know NEXE as a company where ideas are actively promoted and new paths are successfully taken."
The most important consideration for the subsequent joint realization of the innovative bag scanner developed at HAVER & BOECKER, however, is the prevailing need for it at NEXE. “We knew through our contacts in the company that they were looking for a reliable solution that would not only minimize the scrap and error rates, but also detect, document and ultimately eliminate inefficient processes,” summarizes Mirko Hoffmann. "With the new bag scanner from our development department, we had already created the basis and were able adapt it precisely and intelligently to the customer's added requirements.
Already with the order of a 16-spout ROTO-PACKER® RVT SEAL Edition in 2018, the Croatian company had proven its high standards. With its powerful 16 filling spouts, the packer was the first of its kind at the time of commissioning and today it remains the largest possible version within the ROTO-PACKER family. Together with a fully automatic RADIMAT® bag applicator, the packer has ensured optimized production conditions and maximum customer satisfaction since 2019. NEXE d.d. fills three different cements into paper valve bags of 25 and 40 kg. The bagged products are mainly sold directly to the end consumer via DIY stores.
In addition to the HAVER & BOECKER packing line’s outstanding productivity and reliability, the sophisticated and reliable SEAL technology for safe and complete sealing of the bag valves is particularly convincing in Našice. The heart of this technology is a specially designed filling unit that ensures dust-free filling of the empty bags by means of various interlocking functions. The bag valve is welded shut cleanly and securely by means of an ultrasonic sealing unit. The results are clearly visible: an absolutely compact, sealed and cleanly filled bag without product loss.
"The entire production is cleaner than ever before!" Marko Umiljanović, head of the engineering department at NEXE d.d., says enthusiastically. "The benefits are numerous: A clean workplace environment results in healthier work conditions for our employees, less time gets spent on clean-up works and there are immense savings in terms of machine wear and tear. At the same time, the SEAL technology reduces material waste. Most important: our customers are also delighted with our bag cleanliness."
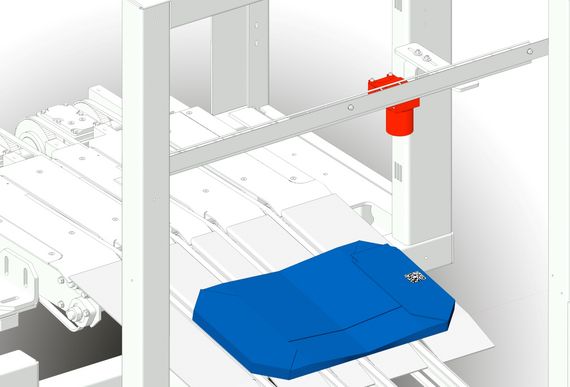
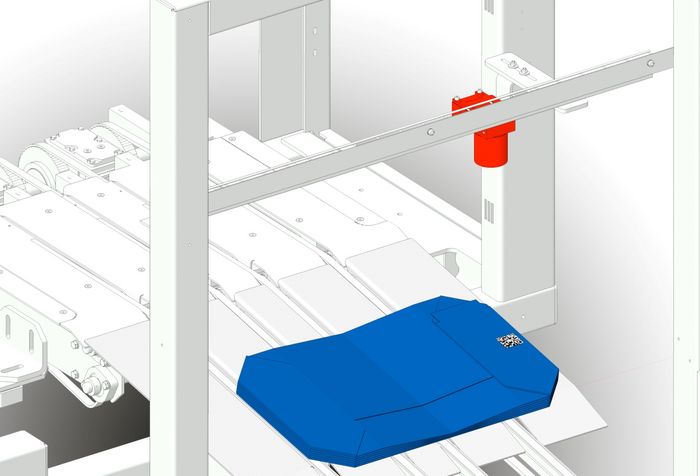
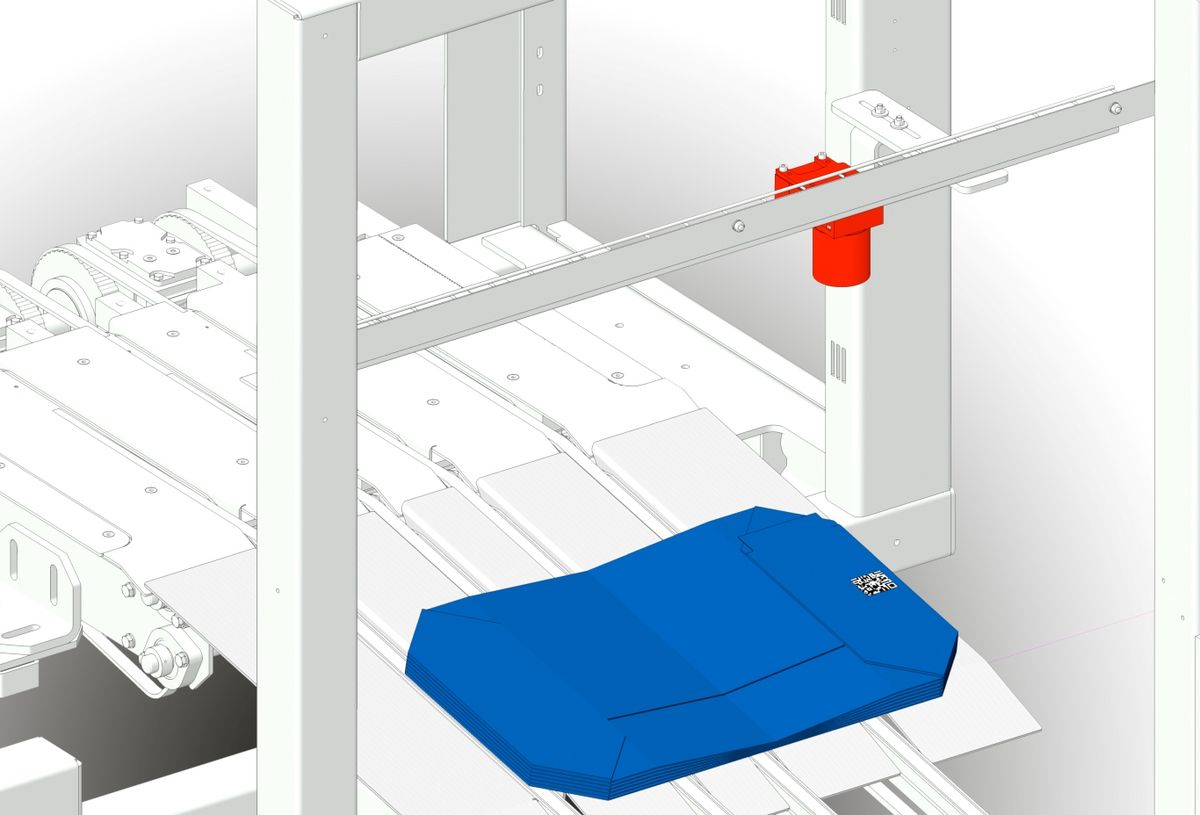
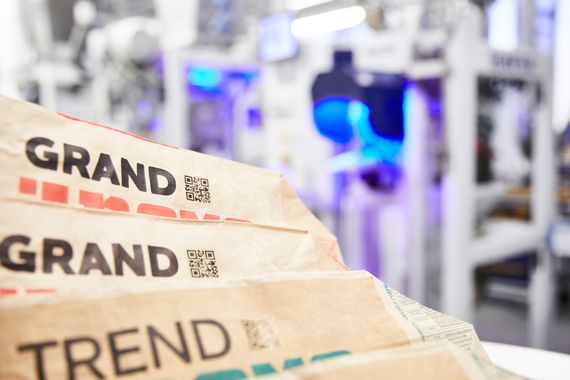
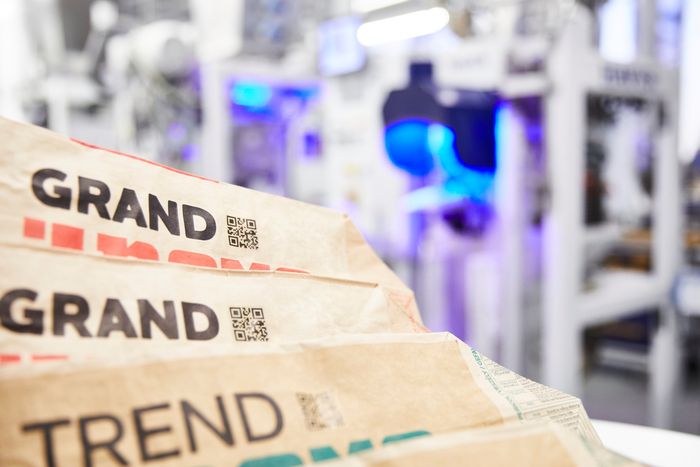
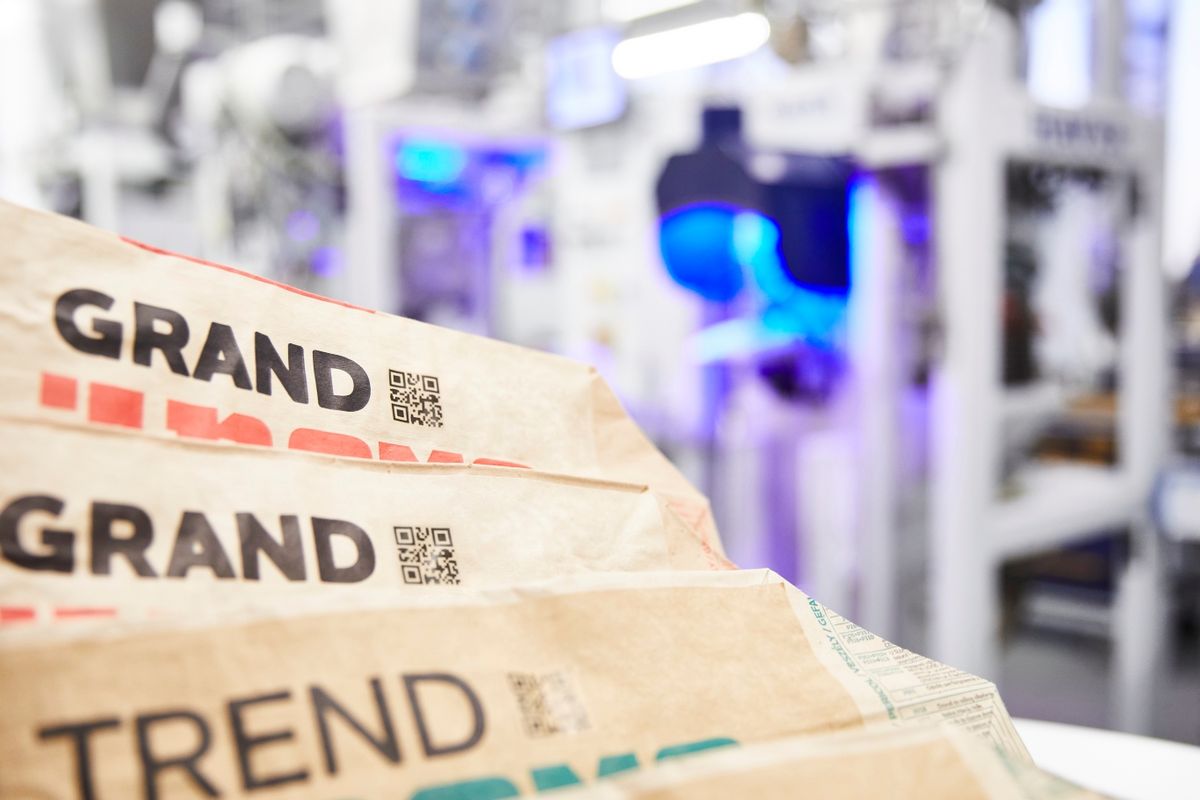
With the idea of the bag scanner, the development engineers from HAVER & BOECKER were met with open ears at the Croatian cement manufacturer. “In the past, the customer repeatedly had to deal with difficulties with the product and bag combination,” explains
Alexander Hering, HAVER & BOECKER sales representative. “Different bags from different manufacturers were characterized by strongly diverging quality characteristics. This resulted in high reject rates and thus an unnecessary waste of resources: from product to increasingly expensive sacks, to labor time and energy costs in production.”
Working closely together, the project participants from both companies defined the individual requirements and the targets of the bag scanner. After a development period of about one year at HAVER & BOECKER, the scanner was integrated into the existing fully automatic RADIMAT® bag opener within a few days and put into operation. QR codes printed on the empty bags identify the respective bag batch, monitor production in real time, and document errors and inefficient processes such as incorrectly placed or broken bags, or deviations in the filling or sealing of the bags.
HAVER & BOECKER electrical engineer Christian Remfert and the NEXE team led by electrical engineers Danijel Koren and Mirko Štefančić - both significantly involved in the implementation of the software - are convinced by the results of the joint project. “In addition to minimizing the reject rate through continuous quality control of bags from different manufacturers and batches, the bag scanner also makes an important contribution to avoiding errors in selecting the right bags, for example when changing the type of bag. The machine recognizes the upper empty inserted bag, checks whether the empty bag stack can be assigned to the product to be filled, and adjusts fully automatically to its dimensions and properties. In addition, if the empty bag stack cannot be assigned to the product to be filled after the scan process, the machine stops automatically, thus completely eliminating a reject rate due to operator error. Thanks to the integration into the on-site ERP system, the bag scanner also enables the bag inventory of each individual product: Expensive and aggravating empty bags are now a thing of the past!”
The new HAVER & BOECKER developed bag scanner is integrated directly into the RADIMAT® bag applicator. Alternatively, HAVER & BOECKER also offers a handheld device for the scanning process. For the hardware, the packaging professionals focus on the greatest possible insensitivity to dirt and high temperatures. However, special importance is attached to the extensive software adaptations, with which the bag scanner can be adapted to the individual conditions and wishes of the customer on site as well as to the respective ERP system.
With the successful operation of the prototype at NEXE p.p. in Croatia, HAVER & BOECKER is setting the course for further deployments of the innovative Industry 4.0 application in companies around the world.
In Našice, they are just as enthusiastic about the measurable optimization of production as they are about the entire project process: "Thanks to the high level of qualification and motivation of all the project participants on both sides and smooth cooperation, all phases of the project were implemented quickly and smoothly. HAVER & BOECKER has once again proven to be a reliable, customer-oriented partner for every need.”