Worth its weight in gold
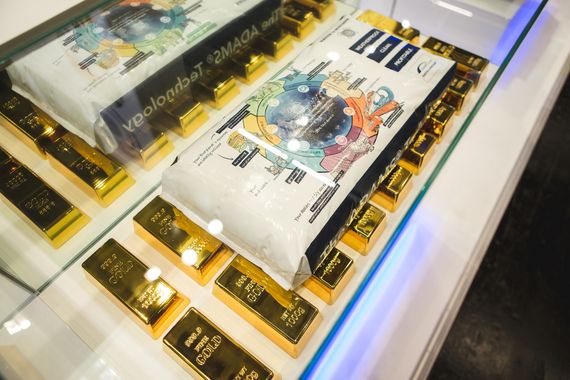
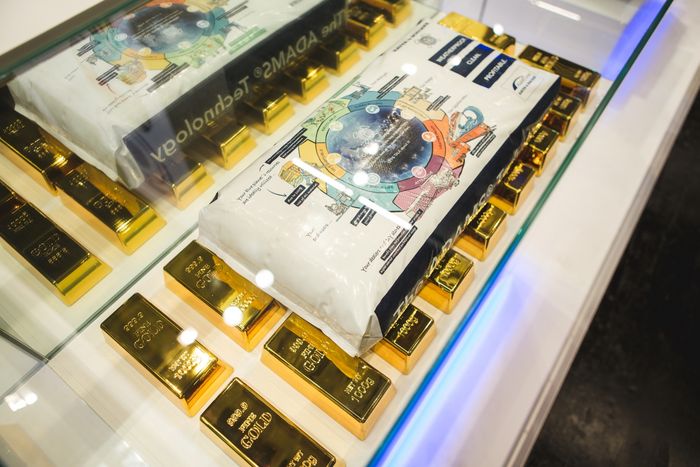
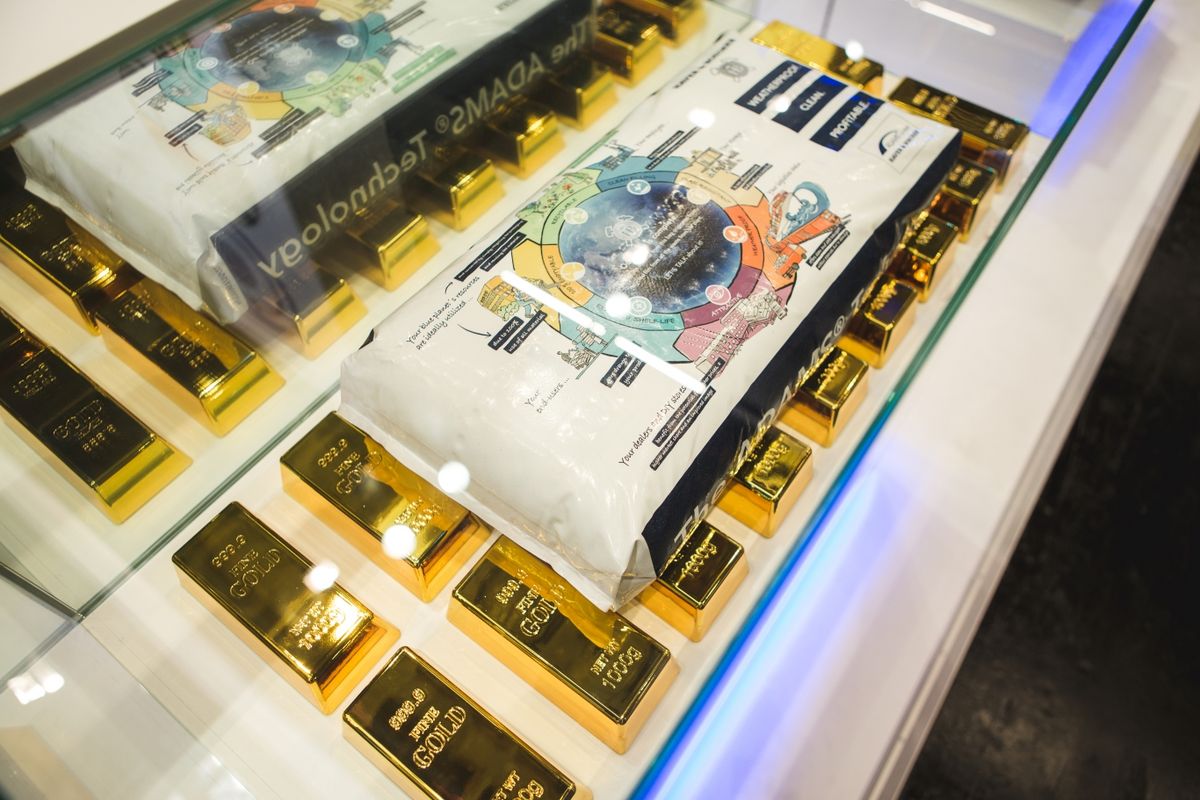
This valuable recycling option is also dormant among our customers. With our ADAMS® technology, they fill powdered products into PE containers. And for good reason: the packaged product is best protected in this way - until it is used by the end customer. The film bags are made of mono-material. Unlike a yogurt pot, where plastic containers have to be separated from the aluminum top, an ADAMS® bag consists of only one directly recyclable material.
In addition, ADAMS® sacks can be completely emptied of residues, making them particularly suitable for recycling. How can this packaging material be returned to the recycling loop as a valuable material?
Do we succeed in collecting the PE bags filled with our ADAMS® systems as recyclable material? We started a self-experiment - and showed that it works! We collected a total of 15 (!) tons of plastic cuttings. These were then processed by Berry Global at the Steinfeld plant and used for the production of new PE bags.
Plastic has a negative image, partly unjustified. If plastic is used as a purely disposable product, it has adverse consequences. Issues such as improper disposal or pollution of the oceans are discussed publicly. It is important to take full advantage of PE and to focus on the true benefits of plastic: the material must be returned to the recycling loop!
Plastic packaging is a functional way to safely protect products. They are recyclable materials that, in the best case, are reused after use:
- Thermal use: they are burned and the energy is used.
- Chemical recycling: oil can be extracted from the material using modern processes.
- Material recycling: They are processed into recyclate and, depending on the quality of the material, used in the production of new films.
The PE bags can be emptied of residues and are therefore easily recyclable. In theory, this is clear to us and our customers. A look at the practice shows: Film packaging is definitely collected and disposed of in a targeted manner. The residual waste container is the most expensive disposal method. The realization that films are recyclable materials is steadily increasing.
Our assessment: 1/3 of the end customers dispose in an exemplary manner, 1/3 could be motivated to do so, 1/3 is rather difficult to access. With our collection campaign, we want to set an example here.
The collection campaign
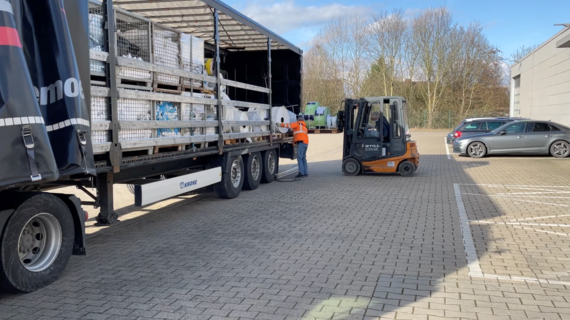
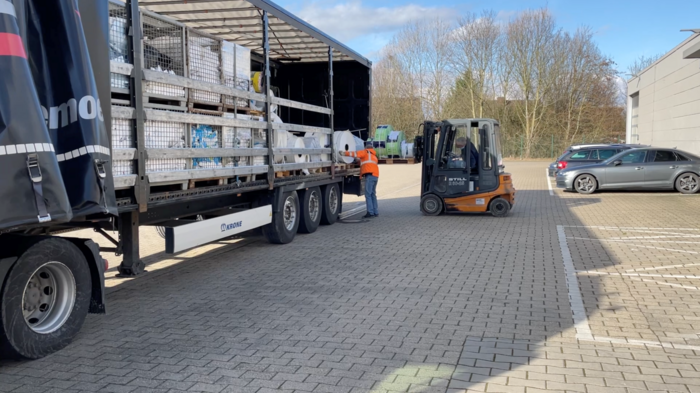
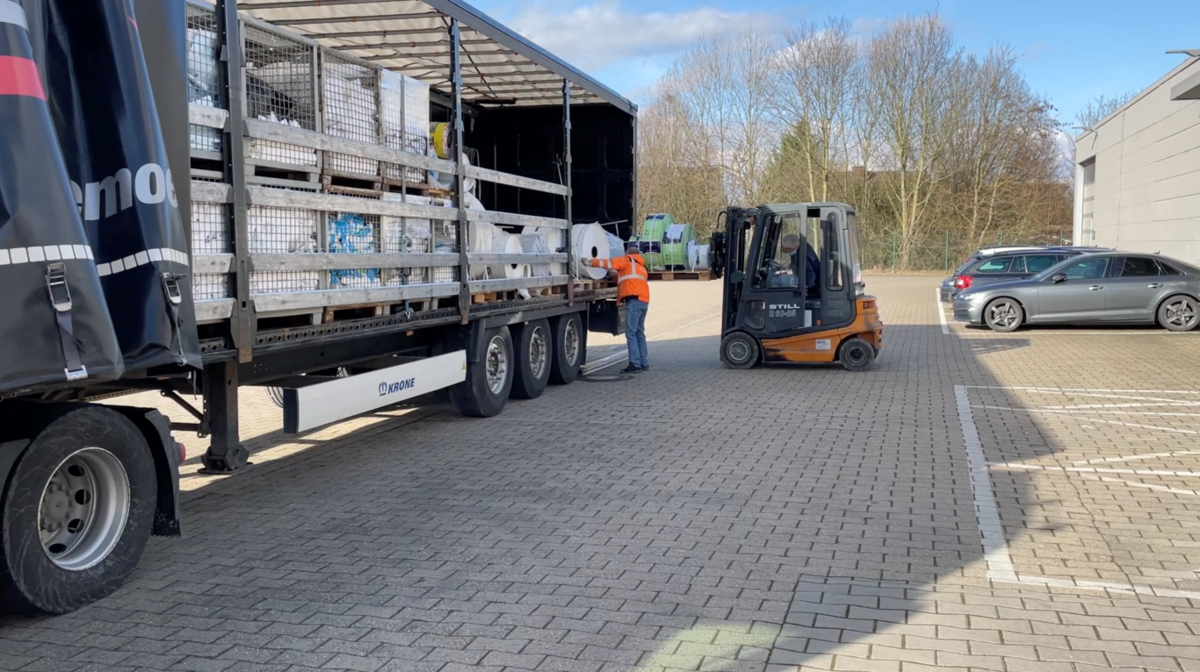
For us, it was now time to show that the foil remnants can be collected and how a new packaging can be created from an old one. In this way, we want to raise awareness that film is a recyclable material and that it is worthwhile to bring it into a cycle.
All machines are adjusted at our factory before being shipped to the customer and go through a test run for final approval. This produces a lot of film remnants that are no longer used and are usually disposed of in the regular way. We have found the way with the film manufacturer Berry Global, one of our long-term partners. The company has its own recycling process for its film products. This was the basis for the possibility of collecting the film scraps and having them further processed. But more about that later!
With our ADAMS® technology, our customers fill powdered products into PE containers. We are convinced that this is a sustainable solution. Background: The bags filled with our ADAMS® technology are made of mono-material, are tear-resistant, long-lasting, resealable, easy to empty and 100% recyclable. The packaged product is thus best protected from the elements. From the filling of the product, to the storage of the bags, to the transport of the product to the end user for application at the point of use, no costly manufactured product is lost.
The reduction of material loss is the decisive and sustainable moment: the CO2 footprint for 25 kg of cement alone, for example, is approx. 14,250 g in Germany (this corresponds to 570 kg CO2 e/t of cement). For every single cement bag that does not "fall by the wayside", the use of plastic bags has been worthwhile! The more valuable product is actually used, the fewer resources are wasted. That alone is sustainable and resource-saving!
Deutsche Umwelthilfe has given it to us in writing: "In principle, reusable bags would most likely be the most environmentally friendly solution here. When new bags are delivered, the empty bags could simply be taken away again and then refilled. If this were not possible, it would be important to pay attention to recyclability and a high level of recycled material in the bags. Composite materials are therefore, in our estimation, rather less suitable. [...] in our opinion, the pure PE sack is the best option if reusability is not possible. In addition, attention should be paid to the lowest possible material use and large filling sizes."
Our customers are convinced of the advantages. In the meantime, more than 200 ADAMS® plants worldwide fill elaborately manufactured powder products day after day. In 2014, we even won the Sustainability Award from Lafarge with ADAMS® , in particular because of the sustainable packaging.
Nevertheless, we, our customers, and also the intermediaries are repeatedly confronted with the thoroughly negative image of plastic. So the same applies here: The material must be returned to the recycling loop!
Our campaign could start. We were delighted to see that all the colleagues involved immediately understood that it made sense to collect this recyclable material. Enthusiastically, they gathered all the foil scraps and collected them in mesh boxes. Months passed until we were faced with a huge mountain of plastic offcuts. Unbelievable what recyclable material was collected in that time! Our forklift driver and the truck driver had fun loading the plastic scraps onto the tractor-trailer. Of course, they wondered what would happen to the material and what would be done with it. Rubber boots? Flower pots? Or a park bench? In any case, the driver set off for his destination with 15 tons (!) of material.
When they arrived at Berry, the film remnants were washed, shredded and processed into regranulate. Then, with the addition of 50% virgin material, a new tubular film was produced for use with our ADAMS® lines. We could hardly wait to see the result. But then the time finally came and we held it in our hands - our high-quality new bag made from 50% recyclate for packaging powdered bulk materials! And at that moment we knew: We have done it, we have closed the loop! With our collection campaign, we showed that collecting and recycling can be so easy and that film is a future-proof and sustainable packaging.
What's special about this bag: we use the layout to communicate the advantages of the PE container at the same time. After all, brand trust is a decisive factor in the purchase decision. The overall composition of a package, consisting of the brand message and a coherent and comprehensible design, can have a decisive impact on the purchase decision. Our "action bag" demonstrates this impressively!
We are optimistic about the future. With the collection campaign, we wanted to raise awareness that film packaging is a valuable resource. Recycling companies gratefully accept this valuable material - we learned this in personal conversations. Recycling is increasingly becoming a prospect; large and successful retail groups even see this as a strategic addition. We are also observing this trend in the building materials sector. For example, Heidelberg Materials, a leading building materials manufacturer, announced the acquisition of a Berlin-based building materials recycling company at the end of November 2022 in order to "significantly strengthen activities relating to the circular economy," according to an announcement. This was followed in mid-December by the announcement of the acquisition of a leading recycling and building materials company in the UK.
Recycling companies everywhere are expanding their capacities, and technology is getting better and more accurate, making sorting and recycling even easier and more possible. On the other hand, disposal will not become cheaper in the coming years.
The legal framework is also setting the direction: As Europeans, we want and need to implement the "Green Deal" presented by the European Commission, including the Circular Economy Action Plan. Recycling rates for all packaging will be increased and continue to increase. Following the plastic levy introduced in the EU in January 2021, member states must now pay 80 cents per kilogram of non-recycled plastic packaging waste to the European Union.
So product manufacturers need to think about optimizing their packaging and pay special attention to recycling processes and rules. As a partner, we are ready to make our contribution!